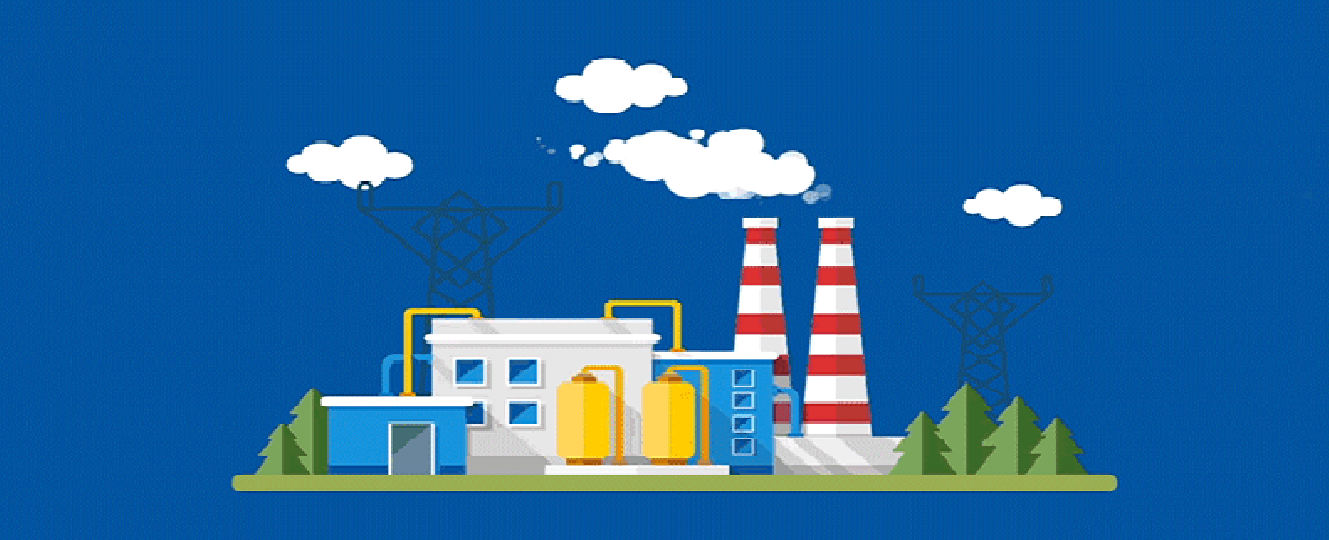
MagnaDrive Upgrades Three Power Generation Applications
MagnaDrive offered MGTL couplings for Minnesota Power’s air pre-heaters as well as a conveyor drive system in San Antonio. The company suggested E-Max couplings for a pump system in India. In all three cases, vibration was significantly reduced and the components benefitted from increased energy savings and value-added features. Learn more about each case study below:
Minnesota Power
Minnesota Power offers a regional power system to northeastern Minnesota. The company supplies electric services to more than 145,000 customers and wholesale electric service to 16 municipalities.
Minnesota Power was experiencing vibration problems on their air pre-heaters. Minnesota Power began re-greasing each coupling during their outages to try to reduce this vibration. Each re-greasing was only effective in reducing vibration for two weeks; each re-greasing tied up three maintenance personnel for an entire day. The company sought out potential products that could solve these manufacturing challenges.
Minnesota Power decided to replace their rigid couplings with MGTL couplings from MagnaDrive.
This was suggested because MagnaDrive Couplings have no physical connection between the motor and the load equipment, there is no vibration transferred between them.
Minnesota Power’s vibration problems on their air pre-heaters were almost completely eliminated. Readings indicated a reduction in vibration of over 80% versus the original rigid couplings. The annual non-energy operating costs using traditional coupling was approximately $21,600, while the operating cost using the MagnaDrive coupling was $3,360. The annual savings per coupling was $18,240. The additional expense incurred per coupling was $5,000.
Breakeven Point = ($5,000) / ($18,240/yr): 0.3 years
National Thermal Power Corporation – India
NTPC Limited is India’s largest energy conglomerate with roots planted way back in 1975 to accelerate power development in India. Since then it has established itself as the dominant power major with presence in the entire value chain of the power generation business.
Pumps at NTPC were continuously drawing 136 kW, which was more than the motor’s rated power and pump brake horsepower at the design point. NTPC accepted the recommendations from MagnaDrive’s partner in India, AVJ Engineering, and placed an order for a MagnaDrive 17.0S FGC E-Max couplings.
The FGC E-Max offers a greater degree of slip to intentionally slow the load speed–typical on variable torque centrifugal pumps and fans. These Fixed Gap Couplings have no moving parts and forgive misalignment, saving critical equipment from vibration. When starting a motor, FGC delays the application of torque to the load, resulting in a cushioned startup—significantly increasing the life of the system.
MagnaDrive estimated a 10 to 15% savings in energy reduction and an operating capacity for the pumps closer to the design condition. After the E-Max coupling was installed, energy use was reduced from 135.61 kW down to 113.54 kW, a savings of 22 kW (16% savings). The vibration levels decreased by 73%.
The City of San Antonio
The City of San Antonio Public Services was experiencing excess vibration in their conveyor drive system. This caused accelerated wear and tear on the equipment.
The city was also concerned about hydraulic fluid spilling from the existing fluid coupling. They installed a MagnaDrive MGTL-18/300 Magnetic Coupling to replace the existing fluid coupling.
After installation of the MagnaDrive coupling system, vibration readings showed an 80% reduction horizontally and a 75% reduction vertically and axially.
The cost savings were also significant:
Operation and Maintenance (O&M) Summary
–Annual O&M costs for Fluid Coupling = $24,000
–Annual O&M costs for MGTL Coupling = $3,800
–Annual O&M savings per coupling = $20,200